Blogs
One can overcome even the greatest of challenges when well-prepared
Hello everyone! I am Oleksandr Bolielyi, and I’m glad to greet you in the new blog post of P-TRAP. Today I will tell you the story of my secondment at Aquaminerals in May-July 2021 in the Netherlands, and how it was managed at this difficult time. I hope that you will enjoy it!
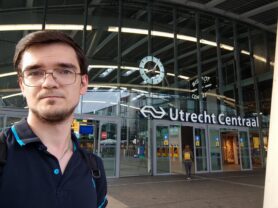
At Utrecht Central station
From the start it was challenging as the goals which I have set for the secondment could not be achieved directly at Aquaminerals. Particularly, what interests me is the production of filter-stable materials from iron residuals. Therefore, after the first annual meeting at the beginning of 2020 I have set an ambitious goal for this secondment: produce the materials with the use of industrial equipment. We have discussed a lot the start of the secondment and decided that the best way to achieve the goal is to process the material at the Calcite Factory in Amsterdam.
At this time I was optimistic enough to think that the processing will be done rather fast (1 month) and the second part of the secondment will be the first steps of new materials characterisation. This was a great opportunity to visit Utrecht University and to conduct experiments with new materials in the lab.
The secondment was postponed twice due to the corona-virus pandemic before I have become assertive in my decision to start despite the COVID-19 pandemic risks.
Starting was the first challenge of mine. It is currently an ordinary thing to be tested before you travel anywhere. After my arrival in the Netherlands, I had to remain quarantined for 7 days. After day 5 of quarantine, you may come for the COVID test to end the quarantine. Obtaining the test results took additional 3 days, but after that, I was ready to start work at the Calcite Factory. Calcite Factory is located in the prodock building in Amsterdam and is known for the production of sand-free calcite pellets that water companies can reuse in their softening operation. The second challenge for me was that the engineers at the factory got really sick and had to undergo various treatments. At the point of my arrival, I had to carry on with what I can on mostly on my own with the support of Aquaminerals.
At the factory the first step of processing was compaction. For this purpose, I was suggested and wanted to try using two machines. The first was a vertical extruder. It is meant to push the material with a screw through a hole or a grid at the bottom. The practical use of it did not yield positive results. When working with such a machine, the constitution is very important. If material is too hard, without pressure it will not pass to the bottom and if the material is too liquid, then compaction will not occur and the material will be spilt after it has passed the extruder.
The second machine I tried is called plate filter press. This machine is used for dewatering materials as well as for compaction purposes with the use of filter-plates. The filter plates are covered with the filter cloths, the pore size of which must be less than the fine particle size in the sludge. This equipment can be risky to operate without proper guidance. Therefore, I had to wait for an engineer to be at the factory to use the filter press.
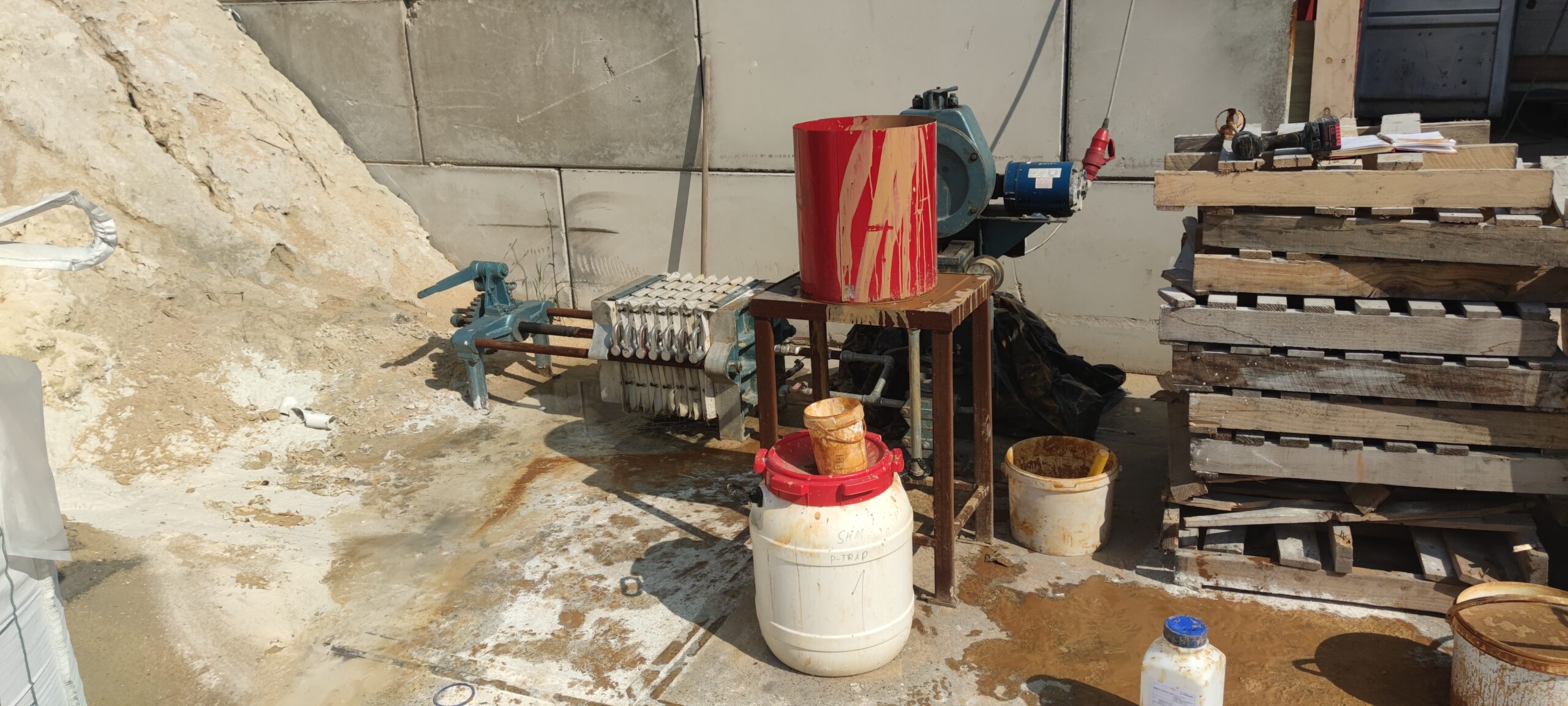
Plate filter press at the Calcite factory
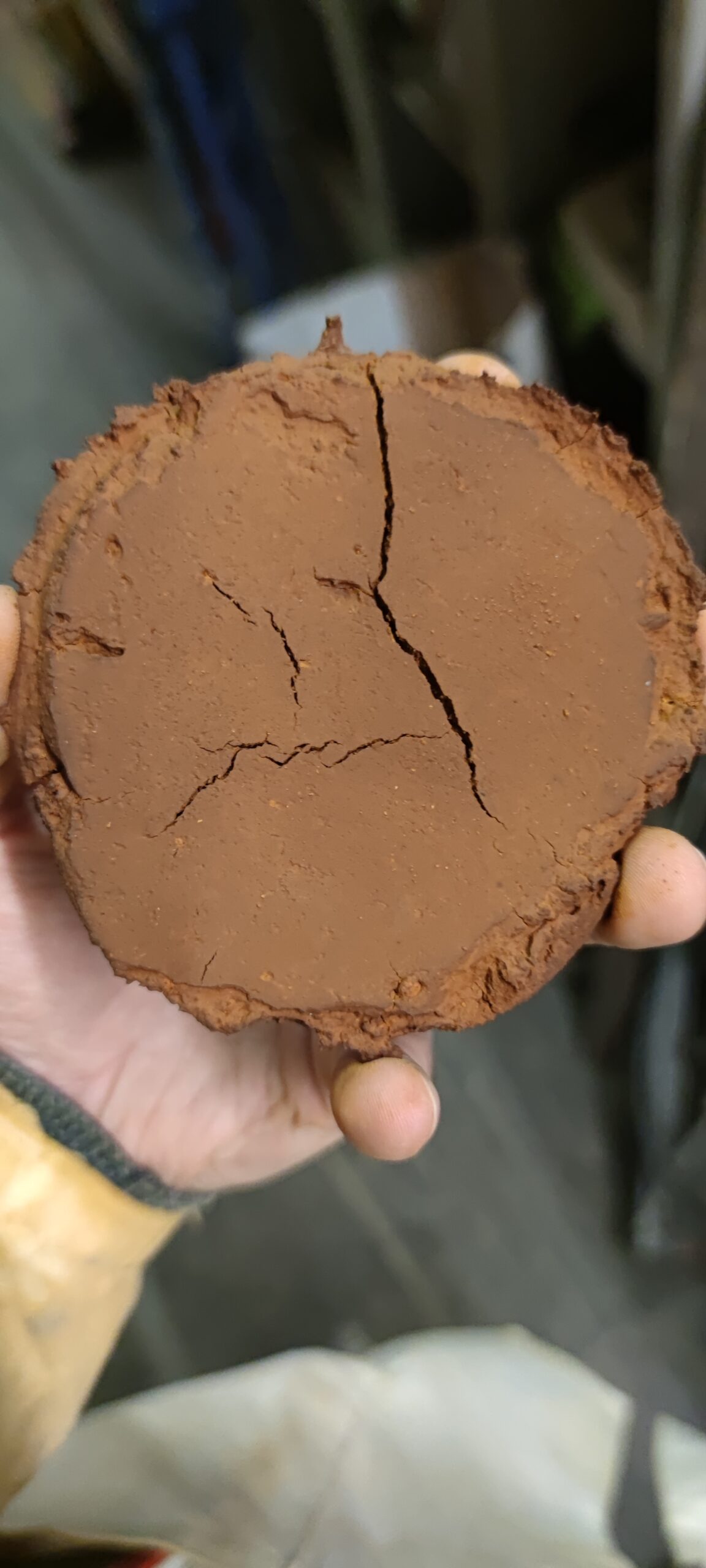
An agglomerated cookie produced by lab-scale agglomeration method
Unfortunately, proceeding as planned was not possible due to the serious illness of the engineer. I felt a bit sceptical by that time how to continue as time was limited, but this was the moment when I had to go on with the alternative route, which is the lab-scale processing of materials. Standard lab method processing resulted in delays in filter-stable materials production. It took around two months to produce enough material, which will later be used in the P-TRAP system. By the beginning of July, I was able to start characterization of the produced materials in the lab of Utrecht University. It was clear that the column experiments, which I have initially planned, cannot be carried out within the time left for the secondment. Thus, it was decided to do the most basic experiments, like batch tests. Within two weeks everything was done and the time for the 5th TSTC and 2nd supervisory board meetings has come. This training week felt amazing and was dedicated to courses stakeholders´ perspectives and development of business plans as well as to updates on the P-TRAP project progress. If you are interested, please check out one of our recent blog posts. My plan after the supervisory board meeting was to check on the status of the engineers and finalize my secondment. I was really lucky to know that the engineer will be one week at the Calcite Factory before going to the hospital. Within one day I have managed to process over 400 L of liquid iron sludge with filter press. After this, the material has to undergo temperature processing. However, this is now the task that will be carried out at GEOS. With the help of Aquaminerals, all the materials were dispatched to GEOS quickly and with this, my secondment at Aquaminerals has come to an end.Travel back home was easy as the government of the Netherlands provided the free tests for travellers until the 31st of August.
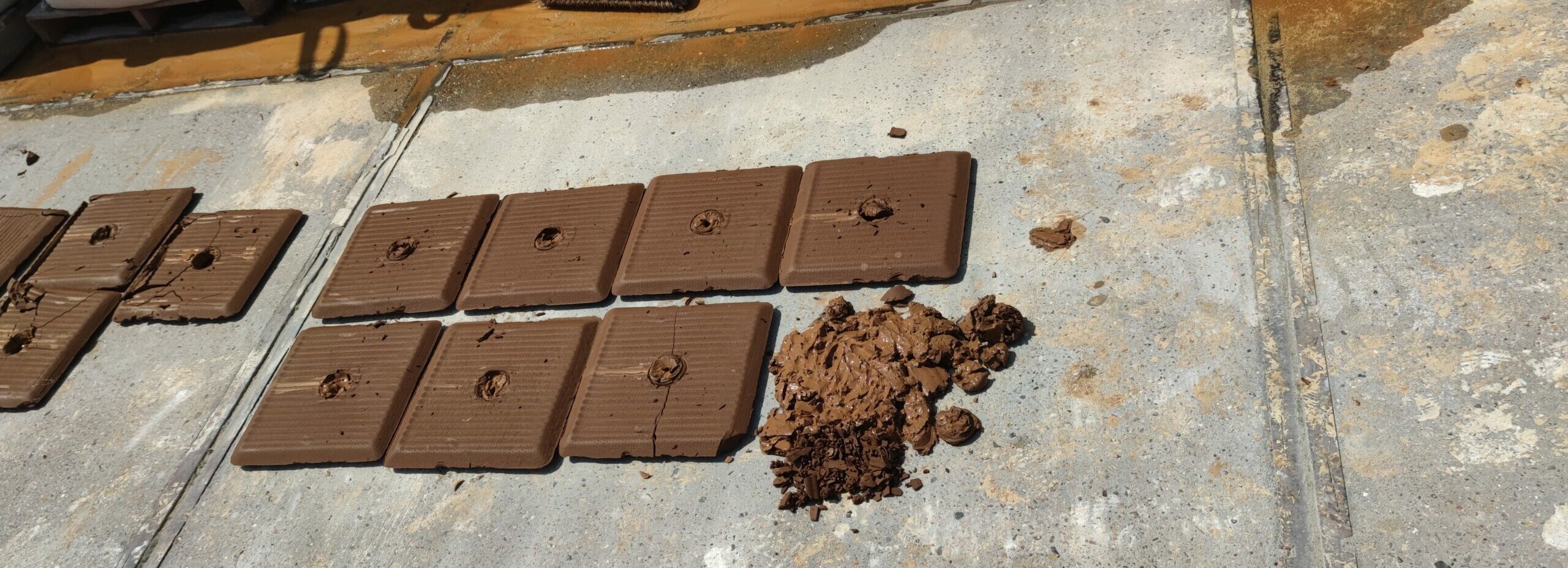
Filter cakes. The final product of filter press processing.
This concludes my story and I am looking forward to finalizing the processing of the material compacted with the filter-press, characterize the materials and prepare for the field campaign in the future.
I would like to acknowledge Olaf van der Kolk for hosting my secondment in Aquaminerals, Wendy Bouma from Aquaminerals who helped to organize the secondment, Leslie Worstenholme for professional guidance at the Calcite factory and Thilo Behrends with the local ESRs: Mingkai, Melanie and Victoria for organizing the lab tests of the materials.
I hope that you have enjoyed and get a positive vibe at these difficult times. I wish you to stay positive and healthy.
Cheers,